Target bonding, the Indium
procedure
This is a
short guideline to bonding of aluminium to copper backing plate. Thermal stress can cause hugh problems with loosing targets. After several tries and
failures a very tough and good solution evolved. This could withstand stress and is never any problems
with. Several other methods have been tested. Several glues and no glue could withstand
the stress. All had failures, were difficult to use and very expensive. The only
disadvantage with the Indium procedure could be if a process is run witch is
sensitive to indium contamination, it should be very careful keeping indium away
from exposed areas. Otherwise at 20 deg
C indium has a quite low steam pressure so contamination should be little problem
when done properly. Also this
bonding is done under air pressure. A
more professional way could be to do this under vacuum, but this has never bin any
problems with trapped air inside the bonded area. Vacuum bonding complicates it
to much and it is usually not necessary for highvacuum applications.
For standard noncritical aluminum mirrors, the target could be
99.95% aluminium from Curt J Lesker or other target supplier.
However 99.5%
"toolshop" aluminium could also be used. This could be purchased from a
metal construction company (tibnor). It is standard
aluminium metal. For standard mirror coatings it is good enough. The indium could be wire 2 mm diameter 99.99%. It is easy to use.
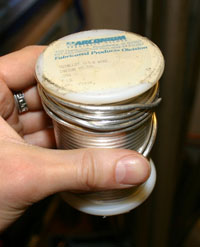
purchased from ebay. (Arconium)
Tools that are useful
A steel
brush, somewhat smaller, size of a toothbrush is better
A steel
scrape
A heat
plate
A scalpel
Procedure:
Separation
of old piece.
The indium
melts at appr 150deg. If an old target is to be separated, there is only needed
to place the backing plate to a heat plate, at slightly higher temperature then
150 deg. After
everything is heated then just slide them apart. No force should be required.
Just slide them apart. It is more difficult to lift them because of the suction. If a new plate,
without In on, are put together or some glued or dirty, they must be carefully
cleaned first, then a thin layer of indium is applied.
Applying
Indium on copper.
If indium
is already on a backing plate from previously runs, then only removal of oxide
is needed. The backing plate is melted on at 160deg C. Until the thin layer of indium melts over the
whole Copper surface. A thin scrape
could be used to remove the oxide. There should be a shining indium surface.
Clean and blank. No oxide should be visible.
"brushing" indium on the copper surface
If the copper
doesn’t have any indium, just pure cupper, then indium must be applied. Due to the
thin soft copper oxide layer, Indium must be “scrubbed” into the surface. This
is quite easily done. At 160 deg. Just melt indium on the cleaned and fresh
cupper surface. Just an easy mechanical
scrubbing with a brush or a scalpel will remove the copper oxide and alloy the
In-Cu. It is important that there is a covering In surface to avoid
oxidizing. No soldering oxide removal should
be used due to the contamination. Just use pure In and scrub it into the Cu
surface. After the whole surface is
covered, use a scraping metal tool or some flat plate to remove residue of
oxides. A blank fine surface of pure indium, blank and silvery should be the
only visible.
Aluminum
surface.
Place the
Sputter target on the heat plate at apr 160deg.
The indium should melt easily on the aluminium surface. Cover the whole surface with indium. Here it is very important to remove the
Al-oxide layer. A very careful
“scrubbing” under the liquid indium surface is done. Use a scalpel or a fine
stainless steel brush.(small size). It is very important to all time cover the
Al surface. A careful scrubbing over the whole surface will get a good alloy in
the surface In-Al. Some In could be
added under the process witch take a couple of minutes. By experience when a
person is doing it, it is quite easy to see the good Alloying of In-Al. the
behaviour of the surface is changed. Never use any Oxide-removal chemicals due
to the contamination.
When the
whole surface is prepared by “scrubbing”, remove the excess of Al-oxide and In-oxide
by scraping the surface with a tool. A clear fine silvery surface, blank and
fine should appear.
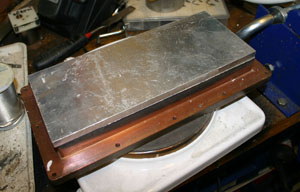
Aluminum target bonded together with the copper
backing plate
Place both
target and Copper backing plate on heat plate. Make sure both surfaces are blank and fine. With a thin liquid In layer
on both surfaces. Both surfaces should now have a good In-alloy in the metal
junction. Place some
extra 1-5cm3 in the middle of the copper backing plate. Carefully
place the aluminium target on the Copper plate and wove it back and forth a
couple of time. Squeeze out the extra of In it should be pressed out between
the plates. The two plates should be easily being moved on the sides. It should
have a very low friction. Make sure In
is squished out all around. If you fell
it went wrong just remove the two plates and start over. Place some extra In
metal on the copper plate and start over. When you
feel there is In contact over the whole plate, align the plates exactly on the
right position. Put some extra weights
on top, 2-5 kg. And shut off the heating
plate. When the
backing plates has cooled, remove excess of In from the target. Use knifes or
some other tool to remove In until a clean surface is available.